Automated, Integrated System Delivers Impressive Accuracies
It was a daunting challenge to find capable machine tools and define a process that would meet demanding accuracy specifications. The original automation solution involved different machines and simple pallet storage. However, as the project at Siemens Ruhstorf evolved, it became an integrated system with three CP 2000 milling/turning centers from HELLER and a multi-level system (MLS) from Fastems.
There are comprehensive standards for protecting people, machines and the environment that have to be met when manufacturing pressure-resistant, explosion-protected electric motors. At Siemens Ruhstorf, these standards are combined with the need for absolute accuracy. Accuracy levels that could only be implemented with a considerable investment of time and money in the old machine park. In addition to this was the need for economical manufacturing required by Rolf Gritl, Industrial Engineering Director at Siemens:
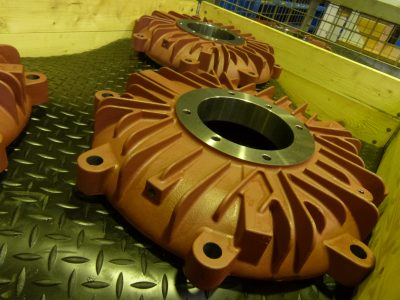
Heller machines and Fastems MLS Multi Level System increase productivity – The highest standards are combined with absolute precision. This means you can achieve IT 6 and better and diameter tolerances of 9.0 µm. This requires the machine to be capable of 4.5 µm.
Firstly a horizontal turning/milling center and a milling/turning center were planned. The first attempts with different providers quickly made it apparent that the best results could be attained with the CP 2000 milling/turning centers from HELLER. So the initial decision was to invest in three machines of this series plus a MLS (multi-level system) from Fastems. Even though turning was more important for these components, the decision was made in Ruhstorf for a milling/turning center. Frank Strothmann, Technological Director at Siemens sees particular benefits in the automation: “The problem is that you have to retool at least one tensioning device per load for the gripper and for loading. With a wide range of parts to be manufactured, the short run times, and the relatively high tool changing times compared to a machining center, I do not regard the horizontal turning/milling centers as an economical solution.”
Due to the high level of part variation, the small batch sizes, the desire to reduce tooling times in mixed operations, and the need to manufacture just-in-time for assembly, automation increasingly became the central focus. And, thus, what was initially a simple pallet storage solution grew into a flexible manufacturing system utilizing a multi-level system (MLS) from Fastems. To put it more accurately: a MLS-LD (low duty) with a bearing capacity of 700 kg per pallet that has space for a total of 72 machining pallets and that integrates two high-precision tooling stations.
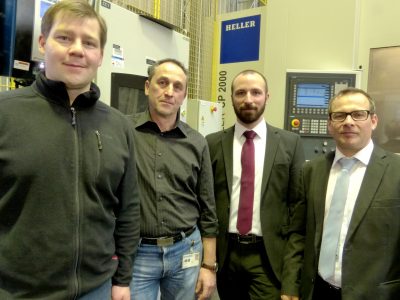
Frank Strothmann, Rolf Gritl, Sebastian Spanfelner and Holger Langer (from left to right): “This project presented a wealth of new findings to us all. The accuracy and economical manufacturing required meant that a completely different concept – one nobody could have foreseen – was developed.” – The MLS ensures that all logistics processes and the continuous flow of information necessary for this are seamlessly integrated into the manufacturing process
Integrated logistics processes for 20,000 spindle hours per year
The centralized pallet handling with integrated loading and unloading stations, and the master computer from Fastems with MMS5 Manufacturing Management Software, at first sound like a standard solution. This was not the case according to Sebastian Spanfelner, Sales Director at Fastems, who regards it as a customer-specific manufacturing system solely due to the spatial requirements: “Neither the entire automation process, nor the reduction of the tooling times nor the interfaces to HELLER were a problem. The MLS ensures that all logistics processes and the continuous flow of information necessary for this are seamlessly
integrated into the manufacturing process. To unload the system or supply it with material, you need adequate space in front of the tooling stations – space that we did not have due to several columns in the hall as well as other factors. However, in spite of the limited space, we managed to make optimum use of the area.”
When working quickly at the tooling and loading stations it is important that the operator knows what to do next. The current orders are therefore stored on the master computer in the Fastems software before production starts. MMS5 plans manufacturing for a period of three shifts in advance. This means that the operator has all of the relevant information on overall manufacturing planning, including all of the tooling information and the resources required before the shift starts. Siemens Ruhstorf, therefore, has a highly transparent automation system that includes order administration, forward-looking manufacturing planning an intelligent NC program and tool administration.
The system has been in production since the end of 2014 and the overall system has achieved an availability of 95 percent. Holger Langer, Area Sales Director at HELLER regards this as the result of the close cooperation with Siemens on one hand and the intensive development work on the other: “We started this project two years before commissioning, and the accuracy requirements were a real challenge for us. For example, we established that turning at 1,000 rpm and high rotary speeds when milling caused evaporation cooling and therefore the cutting fluid temperature control was required to ensure the necessary process stability. If you consider the variation of parts, the small batches, and the integrated system of three machines, this system is without a doubt wholly unique. Where HELLER is challenged in terms of small batch sizes and high flexibility, we have to offer the customer added value with automation. We have our own automation department for this. And, in this case, Fastems was a competent and reliable partner.” The degree to which the tooling times and the main times were improved at Siemens are proven by the 20,000 spindle hours thus far recorded.
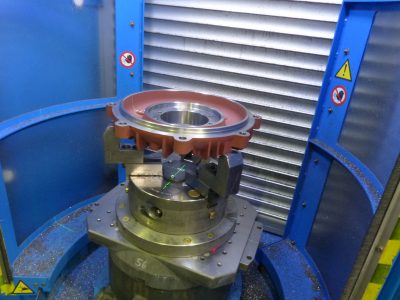
Ergonomic user interface – One of the two tooling stations. The components can be reliably transferred in and out within a radial run-out of 20 µm
Siemens, the Ruhstorf location
The Siemens Ruhstorf location has 1,200 employees and produces explosion-protected motors for industrial fields such as the chemical, petrochemical, oil and gas industries, special motors, low voltage converters for specialist branches (e.g. marine applications, renewable energy) and wind turbines.
The pressure-resistant SIMOTICS XP motors exceed basic safety requirements. The Ex d pressure-resistant model was specially developed to be able to withstand explosion pressure and prevent any sparks that may form in the motor from reaching the surrounding atmosphere.
Interesting side-effects
Unmanned shifts were never the aim at Siemens. The intention was rather to reduce tooling times. Those responsible accepted that this could not be achieved with conventional machines. Today, work is performed with clamping devices fixed to pallets and the component is tensioned on the equipment while on the pallets as required.
Investigations at Siemens have established that due to the evaporation cooling generated at a room temperature of 23 °C during processing and a cutting fluid temperature of 20° C, the components can be cooled down to 18° C within a few minutes.
By the way
With regard to process reliability, the challenge was how to ensure that multiple or inversion measurements can be made while taking the semi-automated processes into account. In addition to easing the burden on the operator and providing additional support for repeat tasks, the Fastems software facilitates the control and monitoring of the production process, and not just the flexible manufacturing systems (FMS). On the basis of the current order and manufacturing situation as well as the resources available (including raw materials, NC programs, tools and their downtimes), MMS5 can undertake forward-looking production planning.
Contact
Siemens AG Industry Sector Mr. Rolf Gritl D-94099 Ruhstorf Tel.: + 49 8531/39-550 www.siemens.com |
Gebr. Heller Maschinenfabrik GmbH Mr. Marcus Kurringer D-72622 Nürtingen Tel.: +49 7022 77-5683 www.heller.biz |
Fastems Systems GmbH Gewerbering 5 D-47661 Issum Mr. Sebastian Spanfelner (Sales Manager Bavaria/Austria) Tel.: +49 162 4080051 www.fastems.com |
"*" indica i campi obbligatori