La perfezione nella pratica
Una strategia dell'”errore zero” e un alto grado di automazione riducono i tempi di riattrezzamento
Quando problemi ed errori nella lavorazione che una volta potevano essere tollerabili raggiungono una certa soglia, è il momento di cambiare qualcosa. È esattamente ciò che ha fatto l’imprenditore Stefan Kempf. Il risultato è un sistema di produzione altamente automatizzato ed estremamente flessibile, probabilmente l’unico nel suo genere nel Paese.
Con un organico di 100 persone, la Norbert Kempf CNC-Technik GmbH di St. Ingbert (Saarland) produce componenti da semplici a molto complessi in lotti da 1 a 500, nonché prototipi per applicazioni pneumatiche e idrauliche, per l’industria automobilistica e per macchine edili. Fondata nel 1970 da Norbert Kempf come officina di tornitura convenzionale, l’azienda ha avuto una crescita continua. Quando Stefan Kempf è entrato nell’azienda del padre, l’azienda si è indirizzata verso la produzione CNC nel 1990. Nove anni dopo, l’azienda disponeva di dieci centri di lavorazione CNC.
La crescita convenzionale ha i suoi limiti
“A quel punto ci siamo resi conto che la crescita convenzionale data dall’acquisto di nuove macchine ha i suoi limiti. In sostanza, più macchine installavamo, peggiore era la nostra produttività. Il personale qualificato, che all’epoca era necessario per il riattrezzamento, era difficile da trovare e l’organizzazione e i processi di supporto diventavano sempre più difficili da gestire. I processi non erano stabili”, afferma il CEO Stefan Kempf. Di conseguenza, sono stati commessi sempre più errori, che hanno richiesto molto tempo, pazienza e spese per essere risolti. Ma non poteva andare avanti così.
“Ero stanco di venire al lavoro ogni mattina e di dover sempre affrontare gli stessi problemi, gli stessi errori e le stesse cause. Ecco perché ho deciso di fare un cambiamento fondamentale”, spiega Kempf, descrivendo la situazione della produzione CNC “tradizionale”. “All’epoca, avevamo circa cinque riattrezzaggi al giorno, 250 trasporti manuali per gli utensili, da 40 a 50 trasporti di utensili a causa dell’usura e una media di sei gruppi di pinze. Tutte queste attività avevano un grande potenziale di errore e la gestione degli utensili in particolare si è rivelata una fonte importante di errori.”
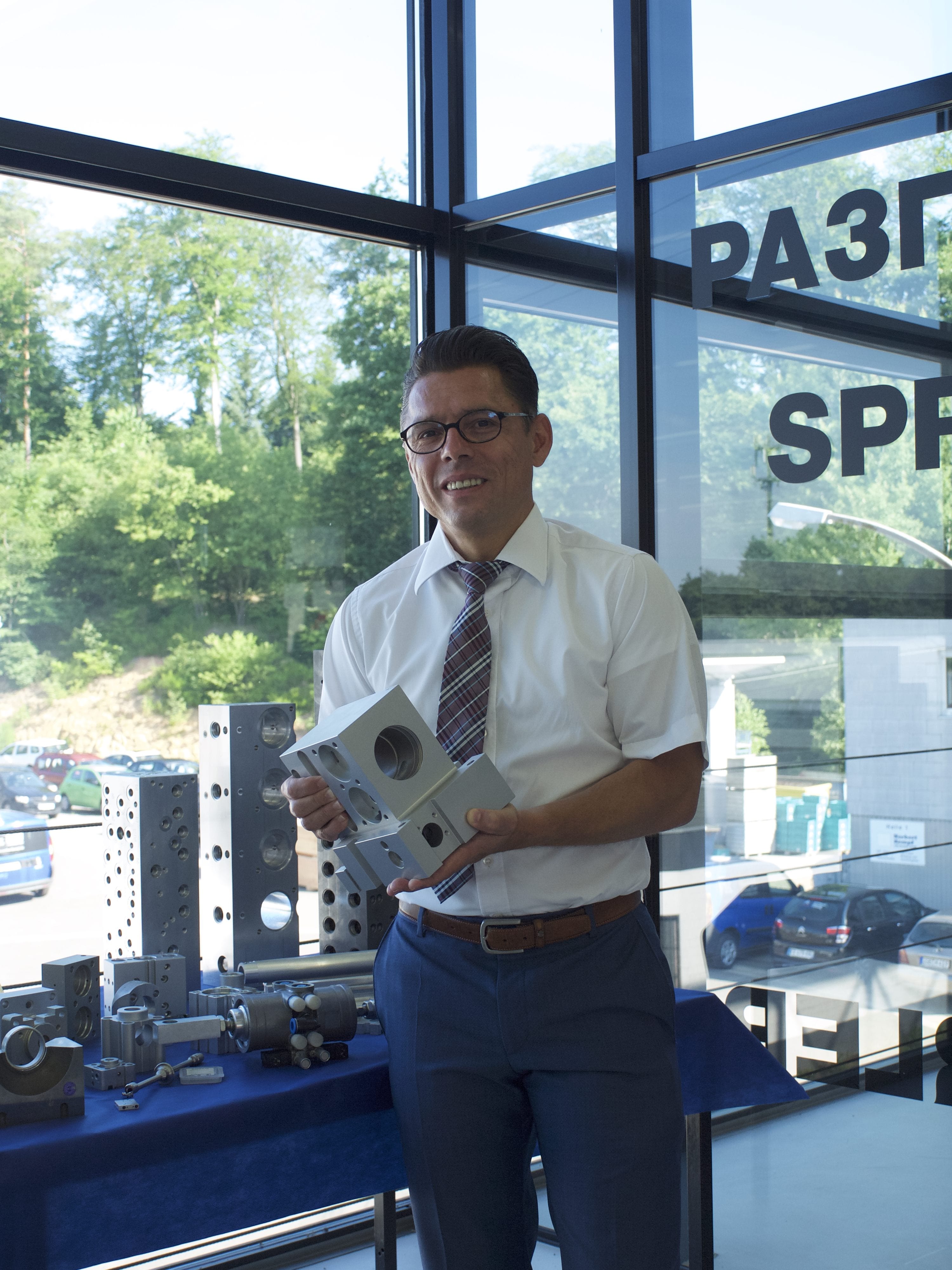
Stefan Kempf, CEO
L’FMS cresce gradualmente
Il problema era come eseguire queste attività senza errori il più vicino possibile al tempo di lavorazione? La soluzione è stata quella di massimizzare l’automazione. Prima però occorreva preparare i processi aziendali chiave. Stefan Kempf afferma: “In primo luogo, abbiamo acquistato un sistema di gestione dei dati degli utensili e abbiamo investito molto tempo nella messa a punto di un sistema completo di gestione degli utensili. Inoltre, ci siamo assicurati di poter produrre noi stessi i pallet di lavorazione e i dispositivi di bloccaggio dei pezzi. Solo allora abbiamo deciso di installare un sistema di produzione flessibile con un sistema multilivello Fastems (MLS)”.
Nel 2003, una macchina esistente è stata collegata all’MLS (con una capacità di 12 pallet di lavorazione). Nel 2011 il sistema è cresciuto gradualmente fino a raggiungere la massima configurazione possibile, con un totale di quattro stazioni di carico e 96 pallet di lavorazione su tre livelli. Oltre alla macchina esistente, sono stati collegati all’MLS altri cinque centri di lavorazione Mori Seiki NH 4000. “Fin dall’inizio abbiamo fatto in modo che le interfacce utensili e i pallet di lavorazione per queste macchine fossero standardizzati e che ogni macchina avesse un grande magazzino utensili con 180 spazi per utensili”.
Gli utensili come fattore limitante
Sebbene l’FMS abbia portato all’azienda un significativo guadagno in termini di produttività, il sistema ha avuto uno svantaggio cruciale secondo Stefan Kempf: “Data la nostra gamma di produzione con lotti da 1 a 500 e circa 18.000 pezzi in portafoglio, il numero di utensili sulle macchine non era sufficiente per eseguire tutte le operazioni di produzione, che erano sostanzialmente dettate dai 96 pallet macchina del sistema, su ogni macchina. Questo significava che dovevamo sempre assegnare un certo pallet pool di pallet ad una macchina specifica”. Un livello di utilizzo della macchina costantemente elevato era quindi impossibile. Inoltre, Kempf sostiene che era presente una serie di fonti di errore che impedivano una produzione veramente affidabile.
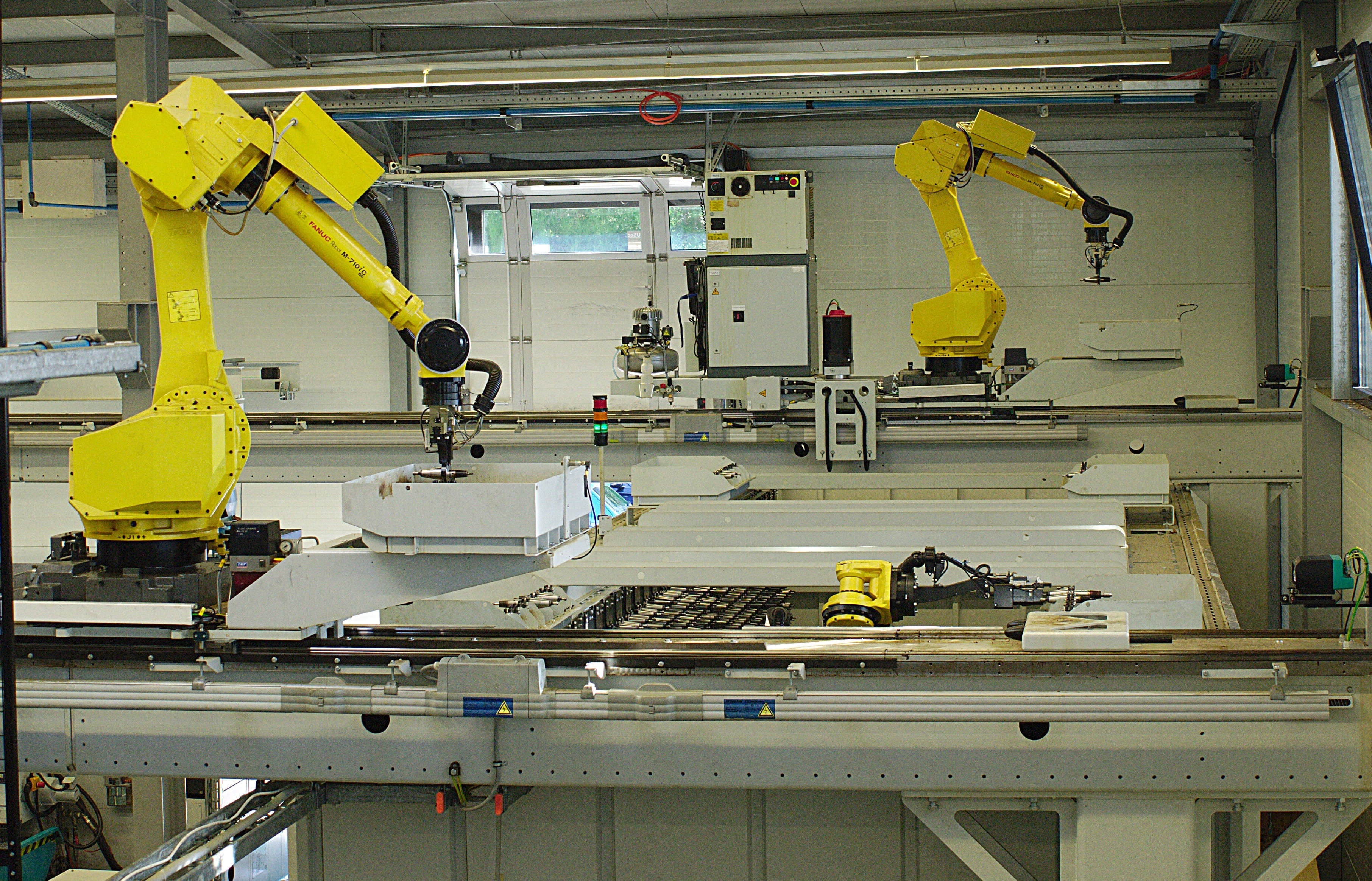
Un magazzino centrale, due linee di produzione, tre robot: un robot nel CTS (centrale) Fastems trasferisce gli utensili ai due robot gantry. In primo piano vi è il robot che alimenta le macchine dell’MLS. Sullo sfondo c’è un altro robot, che trasferisce gli utensili ad altri cinque centri di lavorazione.
Magazzino centrale per 2.500 utensili
Per questo motivo, nel 2013 l’azienda ha investito in un altro FMS Fastems con un magazzino di materiale grezzo, compresa la costruzione di un nuovo capannone. L’MLS-MD (peso medio) con un carico utile di 1.000 chilogrammi per pallet dispone di spazio su quattro livelli per un totale di 156 pallet, metà dei quali sono pallet di lavorazione e l’altra metà pallet materiale. Il sistema, che ora è collegato a sette centri di lavorazione, dispone di quattro celle di carico, ognuna con una stazione di carico per il pallet di lavorazione e una stazione per il pallet materiale. Inoltre, altri cinque centri di lavorazione vengono riforniti automaticamente con utensili dal magazzino centrale utensili.
Una caratteristica eccezionale di questo sistema è la combinazione di un magazzino centrale utensili Fastems CTS, che contiene 2.500 utensili, e di un robot per il trasporto degli utensili. Poiché ogni macchina dispone inoltre di un proprio magazzino utensili con 60 utensili, può accedere a 3.200 utensili. E questo da ogni macchina, perché un sistema gantry con il robot trasporta gli utensili dal magazzino centrale al centro di lavorazione appropriato secondo le necessità. Per l’identificazione univoca degli utensili da parte del lettore del robot, ogni singolo utensile preimpostato è dotato di un chip RFID.
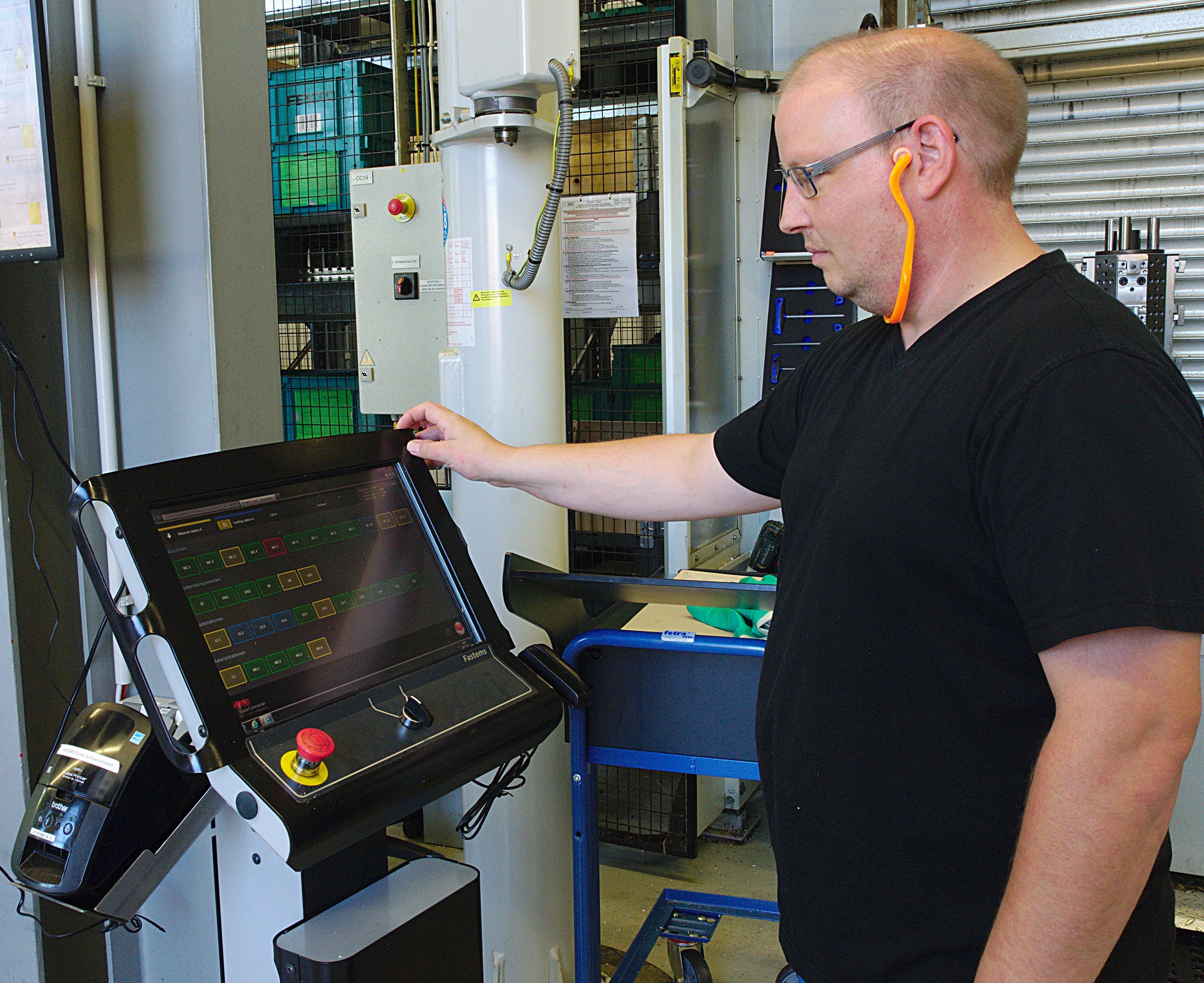
Ogni cella di carico è dotata di un terminale con Fastems MMS. Il software controlla elementi come l’ordine pallet basato sul lavoro nell’MLS e gestisce tutti i programmi CNC e i dati degli utensili.
Il software gestisce la pianificazione e il controllo della produzione
Come principale intelligenza del sistema, il software di gestione della produzione Fastems (MMS) gestisce tutta la pianificazione e il controllo della produzione nell’FMS. Questo include il trasporto robotizzato degli utensili dal magazzino centrale utensili (CTS) alle macchine. Tuttavia, il software non solo controlla la logistica di consegna, in cui pianifica l’ordine dei pallet nel sistema, ma gestisce anche tutti i programmi CNC e i dati degli utensili. Prima di ogni avvio della produzione, l’MMS effettua anche un controllo delle risorse per verificare, tra l’altro, se il materiale grezzo richiesto è presente nel sistema e se gli strumenti necessari per un determinato ordine hanno la necessaria durata di vita. “Se la durata di vita di un utensile non è più sufficiente per la lavorazione, il nostro sistema di assemblaggio e preimpostazione degli utensili riceve automaticamente un messaggio di richiesta dal software”, spiega Kempf, sottolineando: “una delle nostre considerazioni chiave anche prima della messa in funzione del sistema FMS era che i preparativi per la produzione sono di fondamentale importanza per un processo di produzione affidabile. Ecco perché avviamo un ordine di pianificazione del processo per ogni nuovo pezzo o per ogni modifica di un componente. Dall’analisi FMEA, al piano di controllo della produzione, alla progettazione degli utensili e alla programmazione CNC, ogni singolo passo viene pianificato in anticipo, sempre con l’attenzione all’affidabilità del processo”.
Riattrezzamento completamente automatizzato
Con l’ultimo FMS, l’azienda è ora in grado di eseguire ogni attività di lavorazione su ogni macchina, automatizzando completamente il riattrezzamento. “I nostri tempi di riattrezzamento sono in realtà di 0,0 minuti, ciò significa che ogni componente ha sempre lo stesso prezzo per i nostri clienti, indipendentemente dal fatto che ne ordinino dieci o cento”, afferma Stefan Kempf, sottolineando un vantaggio chiave della sua produzione altamente automatizzata e flessibile, mentre altri numeri impressionanti parlano già da soli: Ogni giorno nel sistema vengono effettuati circa 1.000 trasporti di utensili e 500 trasporti di pallet. L’utilizzo medio del mandrino di tutte le macchine è compreso tra il 95 e il 98%.
Spingere l’automazione al limite
“Nonostante livelli di automazione così elevati, da quando è stato installato l’FMS non abbiamo ridotto il personale e dal 2014 abbiamo raggiunto una crescita media annua del 15% con lo stesso organico”, sostiene Kempf, e ci si potrebbe aspettare che sia soddisfatto di ciò che è già stato raggiunto, ma in realtà vuole di più: La flessibilità che otteniamo grazie alla possibilità di lavorare ogni pezzo su ogni macchina dell’FMS è così grande che vogliamo continuare con questo approccio”. Attualmente è in costruzione un nuovo capannone adibito alla produzione. Un altro MLS Fastems vi sarà installato e sette centri di lavorazione orizzontali saranno collegati a quello che ora è il terzo FMS. Attraverso i capannoni, un robot gantry accederà al magazzino utensili del secondo FMS e del nuovo sistema. “Utilizzeremo un GTS Fastems (magazzino utensili gantry) per gli spazi utensili aggiuntivi del nuovo FMS così da guadagnare più spazio nell’area di produzione. Il robot di questo sistema svolge due compiti. Trasporta gli utensili tra il capannone 3 e il nuovo edificio e può anche fornire utensili alle nuove macchine”, afferma Stefan Kempf a proposito della progettazione.
Pubblicato in “Automationspraxis”, edizione 09/2017