Horizontal Machining Plus Automation Prove to Be a Rewarding Investment
Fastems was featured in the Modern Machine Shop’s magazine and blog. The article is a case story about BoatZincs and it’s offshoot manufacturing business Mach Machine and how the companies entered into pallet automation and horizontal machining. According to Mr. Dan Olsen, the President of Mach Machine and Director of BoatZincs, it felt like a jump into the deep end of the pool. However, the overall result was successful.
Originally published in Modern Machine Shop
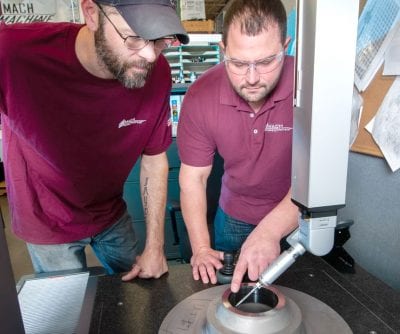
Dan Olsen and shop manager Matt check dimensions of a turbine rotor on the shop’s Hexagon Global 7-10-7 coordinate measuring machine. © Gardner Business Media, Inc.
Quick facts from the article
-
Company: Mach Machine handles prototype and production runs of precision parts for customers in the high-tech, medical, aerospace and military industries
-
Problem: “As the shop’s production mix and volume grew, the time required to construct multiple setups grew as well.” Once Mr. Olsen realized that monthly setups took an employee four hours to complete he decided it was time to invest in horizontal machining. This would allow Mach Machine to design and build fixturing setups on tombstones and leave them in place permanently.
-
Solution: Investing in Fastems FMS ONE with Okuma HMCs, complete with Fastems Manufacturing Management Software (MMS) – the most intelligent software in Industry 4.0. The equipment’s productivity and efficiency allowed Mach Machine to use it for both aluminum and stainless steel parts.
-
Results: Permanent palletized setups increase efficiency and reduce cycle times from 24 minutes per piece to only 10. “The fixturing is designed specifically for the part, so we’re able to utilize the whole work envelope of the machine,” Mr. Olsen says. “Permanent fixturing also gives us excellent part-to-part repeatability.”
The article covers the whole journey from the very beginning to this moment: how the production of the first own products of BoatZincs started, how homegrown metalworking becomes profitable, and finally how the company leaned towards horizontal machining and automation. Modern Machine Shop encapsulated the starting point of taking the first steps towards the change:
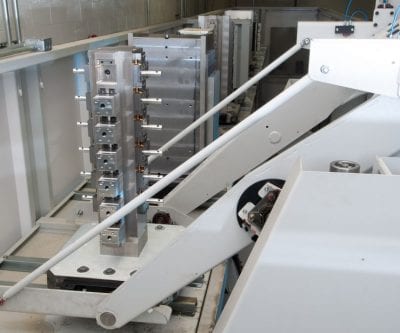
A pallet loaded with fixtured workpieces is placed into the machining queue in the Fastems FMS One. Though in a queue, these might be machined at night or the next day because other jobs have higher priority. © Gardner Business Media, Inc.
“As the shop’s production mix and volume grew, the time required to construct multiple setups grew as well. After watching an employee take four hours to perform a setup that repeated every month”, Mr. Olsen says, “I realized it was time to investigate the use of a horizontal machining center that would enable us to design and build fixturing setups on tombstones and leave them in place permanently.” While Mr. Olsen was researching HMCs, his Okuma representative invited him to a demonstration of an Okuma HMC and a flexible manufacturing system (FMS) from
Fastems LLC. “At the time, I was a little bit taken back because I just wanted to get my feet wet in the horizontal machining area. This was more like taking a dive!” he says. “But I realized that we didn’t have just one job that could go on this machine, we actually had dozens.” The demonstration convinced Mr. Olsen to purchase an Okuma MB-5000H HMC and a 12-pallet Fastems FMS One with an MMS5 control.” Not long after that, the company expanded to 24 pallets and acquired second MB 5000.
The article also mentions Fastems’ tool management system and Manufacturing Management Software (MMS) and explains how they contribute to Mach Machine’s manufacturing processes.
Read the whole story
Please read more from the Modern Machine Shop’s blog post which is a shorter version of the original article published in the magazine: www.mmsonline.com.
All images retrieved from Modern Machine Shop’s original article and rights reserved © Gardner Business Media, Inc. 2019