Focusing on Higher Productivity
The Flowserve Corporation, with headquarters in Dallas USA, has 110 branches in 56 countries, operates worldwide and has concentrated on water, energy, oil, gas and chemicals. The corporation employs 17,000 staff and develops media flow solutions for companies, mainly pumps, gaskets, valves and fittings. The annual turnover is currently around 5 billion USD.
From Stainless Steels to Plastics
“Flowserve has six branches in Germany alone, including Flowserve Essen GmbH with around 180 employees, and manufactures regulating valves and control fittings for the chemical and petrochemical industry. Also, around ten percent of our products are used in the food industry. We estimate that we process around 100 different materials, from stainless steels and so-called “black materials”, i.e. materials that corrode, to titanium, tantalum, cobalt-chromium based hard alloys, aluminum and several types of plastics”, recounts Hans-Jürgen Lübbehusen, group manager for manufacturing at Flowserve Essen. According to him around 45 percent of the products from Essen are for the German market; the rest – approximately 55 percent – is for export.
Cheaper Manufacturing Methods
Flowserve Essen has already amassed experience in automation, e.g. with the horizontal machining center (HMC) that was connected to several pallet stations. “This system was used just for machining aluminum, principally small workpieces. However, the system was sold about two years ago. At virtually the same time, we considered how we could manufacture larger components and differing materials cheaper, with a view to establishing the company on the market, for the long term. In this context, we were looking for a highly-efficient machine that would give us the option of clamping the workpiece just once for machining, because until now these types of components were produced, depending on the machining required, on different systems. This, of course, meant that the clamping procedure had to be repeated several times which was very time consuming, Hans-Jürgen Lübbehusen recalls.
Looking at Automation from the Outset
Flowserve Essen consciously took its time to decide which machine to opt for, as the new system was intended as an investment in the future. Here’s what the group manager for manufacturing had to say: “From the very beginning we agreed that the new horizontal machining center should be connected to an automation solution so that, if required, an unmanned third shift could be introduced.”
Finally, the choice was made for the horizontal machining center DBF 800 from Heckert, which allows the complete machining process to be performed using just a single clamp, where the TDM (turning, drilling and milling) principle is the deciding factor for the productivity level of the manufacturing system. The work spindle of the TDM head performs all of the machining operations on the clamped workpiece.
An HMC including FPC from a Single Source
“The DBF 800 provided us not only with a high-performance machine that offered a range of options for manufacturing, but also a tailored automation solution, whereby the machine manufacturer recommended the Fastems FPC-3000” as underlined by Hans-Jürgen Lübbehusen.
The flexible pallet container was first introduced by Fastems in 2012. Having a length of 11.5 meters and width of 3.6 meters, it offers sufficient space for machine pallets in the nominal sizes of 800 x 800 mm as in Flowserve’s case or 1,000 x 1,000 mm. The maximum load per pallet including the machining pallet is 3 tons. The FPC is designed for heavy workpieces and transforms a machining center, like the Heckert DBF 800 into a space-saving, flexible manufacturing system.
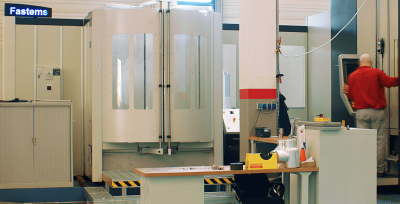
Huge increase in manufacturing productivity with unmanned production
Not a Classic Mass Production Manufacturer
High levels of automation with concomitant flexibility in manufacturing is a fine thing but not always feasible ad-hoc, as company director Peter C. Berger knows only too well. “We already knew, before the installation of the complete system in August 2013, that the goal of a third unmanned shift was not going to be feasible straight away. We decided, therefore, to set a timescale of one year, in order to make all the necessary preparations.”
The statement of the managing director is only too understandable, as Flowserve is not a classic mass production manufacturer, as Hans-Jürgen Lübbehusen stressed: “Around 60 percent of our products are specific to the customer and, occasionally, they are unique. Due to the very high diversity of components, we have to prepare the NC programs with a great deal of care for differing workpieces and run the HMC to produce these components. In addition, the machine operators need to have a greater degree of familiarity with the system as a whole. This all requires time, and should be approached with regard to process security and as a result product quality, therefore, it should not be rushed. If there is a large pool of NC programs that have been run on the HMC, concrete ideas on implementing a third unmanned shift can be considered.”
A Fourfold Increase in Productivity
Flowserve Essen has already achieved initial, concrete improvements in productivity using the HMC. Peter C. Berger gives an example: “Previously, to manufacture one aluminum angled housing we needed an entire shift, as we had to perform many differing manufacturing processes in parallel, such as turning and drilling holes, on separate machines. Now we can perform the required operations on four of these angled housings in a single shift. To do this, two angled housings are processed in a single clamp on the HMC.” The labor time required for this workpiece alone has been reduced by 75 percent.
“Additionally, the idle time of the components has been minimized as re-clamping for operations on other machines is no longer required” says Hans-Jürgen Lübbehusen, adding: “We recognized this potential beforehand, and this gave us a sound argument for making the investment in the HMC and the FPC-3000. Of course, there will always be workpieces that, simply due to the material strength, will require longer spindle run times and therefore not offer the same potential for savings. Nevertheless, we are still confident that we will be able to achieve production time savings in the region of 25 to 50 percent, even for components of this type.”
Investment with Great Potential The current automation solution leaves Flowserve Essen ideally prepared for the future, says company director Peter C. Berger: “All of the pallet places are currently occupied, when possible, and the machining pallets are fed into the machine by the FPC, depending on the job and delivery deadline. Two employees on a single shift are currently responsible for loading the jig. Soon we will change over to a two-shift system. The next step is then the unmanned third shift. If we reach the capacity limits of the current automation system in a few years, we can extend the FPC-3000 by up to 12 additional pallet places and connect a further HMC, as required.”
“The horizontal machining center has provided us not only with a high-performance machine that offered a range of options for manufacturing, but also a tailored automation solution, whereby the machine manufacturer recommended the Fastems FPC-3000 to us,” explains Hans-Jürgen Lübbehusen.
Related products:
"*" indica i campi obbligatori