Importante passo verso l’automazione alla Doesburg Components
Doesburg Components, parte del gruppo Gietburg, investirà notevolmente per ampliare la sua produzione nel corso dei prossimi anni. I lavori sono già iniziati con una speciale cella robotizzata che elabora i componenti in ghisa per i sistemi di frenatura degli autocarri, e negli anni a venire verranno aggiunte altre celle robotizzate. Doesburg Components intende produrre una quantità superiore di prodotti con il medesimo livello di personale, cosa che sarà possibile soltanto con un elevato grado di automazione.
“Vi sono tre ragioni importanti alla base dell’automazione”, spiega Jos Smeets, Direttore di Doesburg Components. “Il primo è il salario orario relativamente alto in Europa, il secondo è l’onere fisico che grava sugli operatori e il terzo è la netta mancanza di personale altamente qualificato. Nel 2009 stavamo raggiungendo il 60% di fatturato in meno, ma ora stiamo raggiunto la piena capacità produttiva e gli operatori CNC sono difficilissimi da trovare. Dei 10 CV ricevuti c’è da sperare che almeno uno di essi sia di una persona con sufficiente esperienza, questo per dire quanto sia difficile.” Negli ultimi anni, Doesburg Components ha aumentato notevolmente il numero del personale passando da 60 a 103 persone. “Ma un’ulteriore crescita deve arrivare principalmente dall’automazione”, spiega Smeets. “Abbiamo sfruttato la crisi economica per entrare in contatto con nuovi clienti che desiderano acquistare moltissimi prodotti sia attualmente che nei prossimi anni. Il numero di prodotti dei sistemi frenanti che vengono lavorati con la nuova cella robotizzata è stato fissato a 150.000 pezzi all’anno, tuttavia, il cliente ha già aumentato questa richiesta a 240.000.”
Investimenti
Doesburg Components ha altri grandi progetti in programma. L’azienda intende investire notevolmente nell’ampliamento dei suoi macchinari. Smeets continua: “Il 2011 sembra che sarà un anno migliore del 2008. È adesso disponibile una nuova generazione di autocarri e motori diesel, con parti sempre più complesse. I nostri ingegneri si recano regolarmente presso i nostri clienti per lavorare all’ideazione di nuovi progetti per i nuovi componenti. È solo così che si riesce ad ottenere una lavorazione completamente automatizzata al prezzo di costo complessivo più basso possibile”. Per assicurarsi che l’azienda sia pronta per la futura quantità di prodotti, Smeets intende investire circa 10 milioni di euro in nuovi centri di lavorazione robotizzati e automatizzati nel periodo compreso tra il 2011 e il 2015. “Ma poniamo requisiti rigidi ai fornitori dei robot e delle macchine”, sottolinea Smeets. “I tempi di operatività nell’industria automobilistica sono estremamente importanti, quindi acquistiamo macchine solo da fornitori in grado di fornire un servizio rapido. Non possiamo trovarci ad aspettare un giorno intero per un ingegnere.”
Due robot 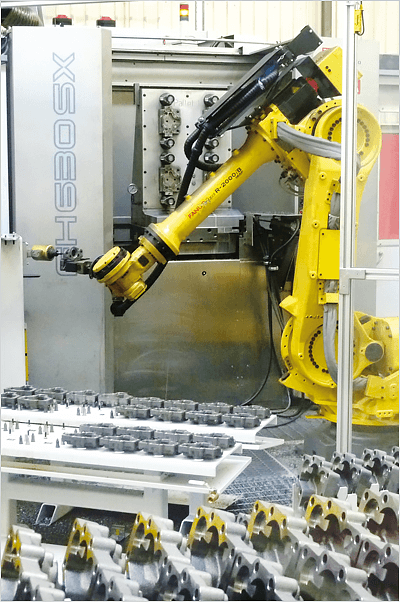
Dopo la lavorazione, il robot effettua la sbavatura dei pezzi prima di restituirli alla stazione materiale. L’ultimissima cella robotizzata è la prima parte del nuovo investimento. La cella robotizzata comprende due centri di lavorazione, un centro di lavoro verticale Quaser MK603S e un centro di lavoro orizzontale Toyoda FH630SX. Le macchine sono state fornite da Alfred van Meegen e Toyoda Europe a Krefeld, Germania, mentre Fastems si è occupata dell’automazione e della fornitura completa del progetto chiavi in mano. Quaser e Toyoda sono posizionati agli angoli destri l’uno rispetto all’altro. Vi sono due robot, uno di fronte a ogni macchina. Tra i due robot vi è una tavola tampone sulla quale vengono posizionati e prelevati i prodotti. “Ciò è importante per la produttività”, spiega Henk Kremers di Valkworks. Valkworks è il rappresentante di Fastems nel Benelux. “Il nostro progetto si è basato sul prodotto del cliente. Il prodotto deve essere lavorato su due lati? Deve essere lavorato orizzontalmente o verticalmente? Quanto è lungo il tempo di lavorazione del prodotto e qual è il tempo di manipolazione del robot, compresa la sbavatura? Dopo aver esaminato tutti questi aspetti abbiamo deciso che un solo robot non sarebbe stato sufficiente in quanto non sarebbe stato in grado di tenere il passo con i centri di lavoro. Così abbiamo deciso di utilizzare due robot, con una tavola tampone tra di loro”.
Alta velocità
Anche i due robot Fanuc non sono in grado di stare al passo con Quaser e Toyoda. Sono costantemente in funzione. Il primo robot di fronte al Quaser, preleva pezzi in ghisa non elaborati dalla stazione materiale. Quattro pezzi sono fissati uno alla volta sull’attrezzatura su Quaser. Dopo la lavorazione, i pezzi vengono sottoposti a sbavatura dallo stesso robot quando ancora sono bloccati sull’attrezzatura. Successivamente il robot posiziona i pezzi sulla tavola tampone. Il secondo robot preleva i pezzi dalla tavola e li fissa sull’attrezzatura su Toyoda. A questo punto è stato lavorato solo un lato del pezzo. I quattro pezzi sono fissati uno alla volta anche su Toyoda, il quale lavora l’altro lato dei pezzi. Una volta lavorati, il secondo robot preleva nuovamente i pezzi uno ad uno e procede alla sbavatura. I pezzi finiti sono quindi riposizionati sulla tavola tampone dalla quale il primo robot li preleva e li riporta alla stazione materiale. Il ciclo di lavoro si ripete continuamente. Tra i due robot vi è una porta che generalmente resta aperta. La tavola tampone è suddivisa in due metà tra le quali può scorrere la porta. Kremers spiega: “La porta fa parte del sistema di sicurezza. Se una delle due macchine è fuori uso per le misurazioni o per una piccola manutenzione, l’altra cella robotizzata può ancora lavorare da 10 a 12 parti. È importante mantenere i fermi macchina ad un minimo assoluto”.
Complessità
Oltre alla potenza della cella robotizzata, la sfida più grande di questo progetto chiavi in mano è stata l’integrazione del software robot con il controllo della macchina utensile. -Kremers continua: “La cella robotizzata è stata progettata per lavorare circa 30 parti all’ora, da semilavorati in ghisa a prodotti finali completamente lavorati e sbavati. Ciò significa che il robot controlla la macchina. Il robot dice alla macchina quando può iniziare la lavorazione. Inoltre, è importante che i robot non si scontrino mai tra loro”. -Fastems si è occupata dell’intero processo di integrazione, compreso il software. L’armadio di controllo è dotato di una connessione remota alla sede Fastems in Finlandia e qualora dovessero sorgere problemi, questi verranno risolti immediatamente dal quartier generale. “Quando la cella robotizzata è stata consegnata a Doesburg Components, ha iniziato a funzionare bene sin dall’inizio. Abbiamo dovuto semplicemente prepararci in modo approfondito e sapere ciò che il cliente voleva”, conclude Kremers.
Scritto da Paul Quaedvlieg
A proposito di Doesburg Components
Doesburg Components di Nieuw Bergen lavora principalmente sulla fornitura e sempre di più sullo sviluppo e sulla progettazione di componenti pronti per l’installazione (componenti in ghisa e componenti in ghisa elaborati) per il settore agricolo e dei trasporti internazionali. I componenti sono forniti ai clienti tra i quali si annoverano DAF, Deutz, Leyland Trucks, Daimler, MTU, Wabco, Lely e McCormick. Doesburg Components fa parte del gruppo Gietburg, che comprende inoltre Modelmakerij Hengelo, Gieterij Doesburg, Cirex in Almelo, Gietburg e la recente acquisizione Arbin Components di Venlo.