Automazione all-in-one, incluso il cambio di configurazione – Cella robotizzata agile per la movimentazione di pezzi e pallet
Si trattava probabilmente di uno dei progetti di automazione più ambiziosi finora realizzati da ALLMATIC-Jakob Spannsysteme, qualcosa di probabilmente inedito e unico nel suo genere, ovvero la creazione di una cella robotizzata per la movimentazione di pallet e pezzi. Uno degli aspetti particolarmente impegnativi è stato il desiderio di automatizzare il cambio di configurazione di una macchina per poter gestire la produzione 24 ore su 24.
La ALLMATIC-Jakob Spannsysteme GmbH sviluppa e produce morse per macchine, da morse ad alta pressione per fresatrici convenzionali a soluzioni complesse per centri di produzione flessibili. Progettano inoltre soluzioni appositamente studiate per esigenze particolari. Secondo l’Operations Manager Herbert Mayr, ALLMATIC-Jakob Spannsysteme è tra i fornitori leader nel loro settore. Tuttavia, per diventare leader del mercato, l’azienda non mira a vendere più morse dei suoi concorrenti.
Mayr afferma: “Piuttosto, ci stiamo sforzando di diventare leader tecnologici nel nostro segmento entro il 2030. Nell’interesse dei nostri clienti, dobbiamo sviluppare continuamente prodotti innovativi, aggiungere soluzioni più intelligenti e, soprattutto, concentrarci intensamente sull’automazione. A questo proposito, uno dei nostri progetti più ambiziosi è stato lo sviluppo e la realizzazione di una cella robotizzata automatizzata per realizzare fino a 32 diversi componenti per morse in singoli lotti di oltre 100 unità per ordine, 24 ore su 24. La cella non si limita a combinare la movimentazione di pallet e pezzi all’interno di un unico sistema, bensì si occupa anche del cambio di configurazione non presidiato della macchina”.
Date le grandi aspirazioni, molti responsabili operativi di altri produttori di macchine hanno inizialmente scosso la testa, dice Mayr e aggiunge: “Questo fino a quando non ho incontrato il Senior Sales Manager della Fastems, Thomas Weinhold, in occasione di una fiera interna della Gebr. Heller Maschinenfabrik. Le sue domande molto specifiche mi hanno fatto capire che mi ero imbattuto in qualcuno che aveva capito veramente quello che stavo progettando. Per farla breve: insieme a Fastems ed Heller come fornitore di macchine e appaltatore generale del progetto, siamo riusciti a realizzare l’idea di una cella robotizzata”.
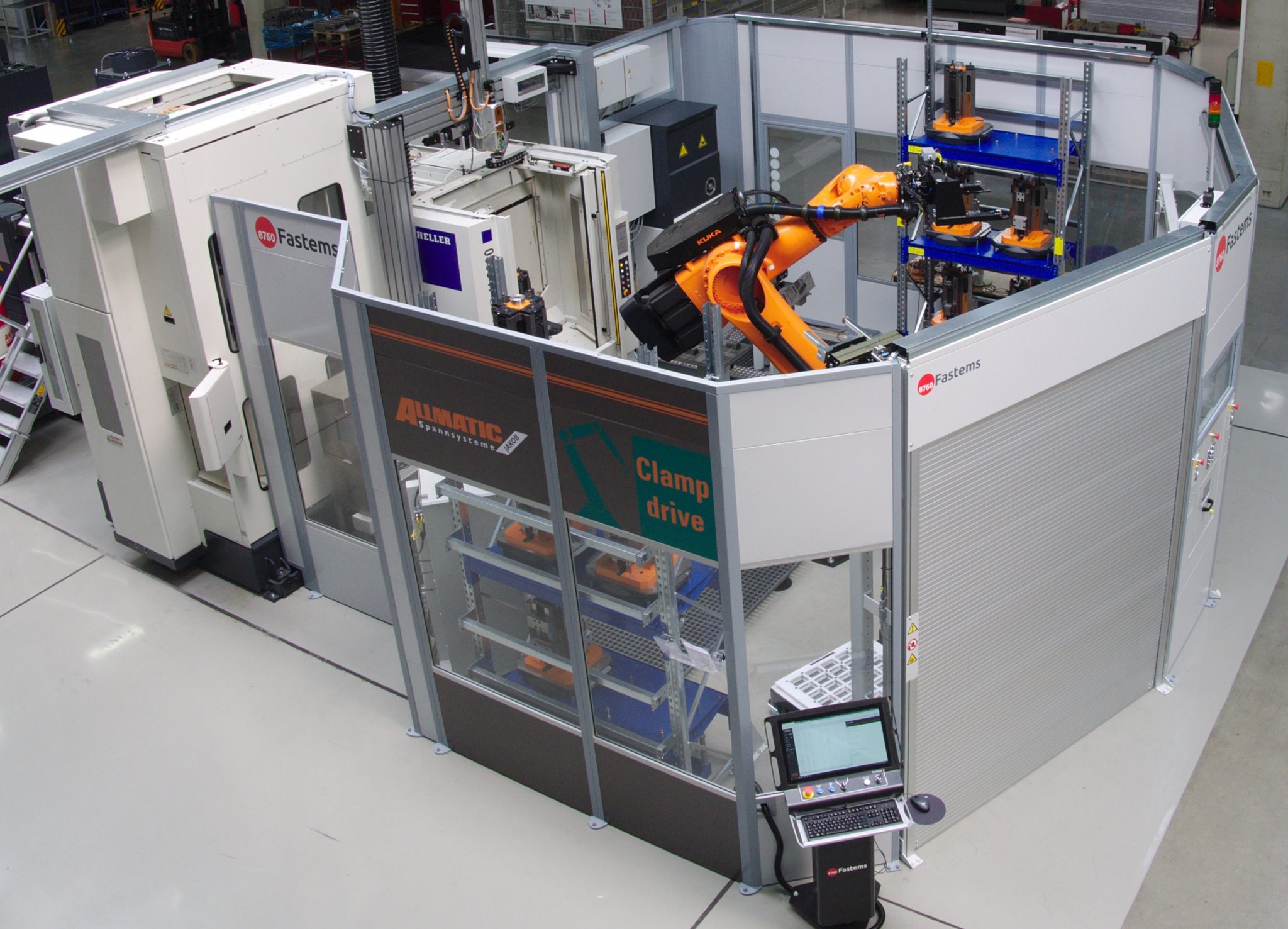
Questa cella robotizzata, che ALLMATIC utilizza dal 2018, è unica e presenta diverse caratteristiche speciali.
Inizio della produzione tramite codice a barre
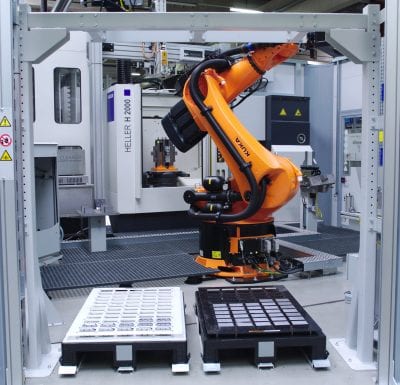
Una delle due stazioni di materiale, ciascuna per 2 europallet in plastica per pezzi grezzi e finiti.
I singoli componenti della cella robotizzata (vedere riquadro: cella robotizzata agile) e, in particolare, la descrizione del tipico processo di produzione, fanno un po’ di luce su ciò che rende questa soluzione di automazione così speciale.
Luis Paiba, responsabile dello sviluppo e della progettazione di ALLMATIC spiega: “Su entrambi i lati delle stazioni di materiale sono presenti 2 pallet ciascuno per materiale grezzo e pezzi finiti, in modo da poter realizzare senza sorveglianza fino a 2 ordini diversi, compreso il cambio di configurazione della macchina completamente automatizzato”.
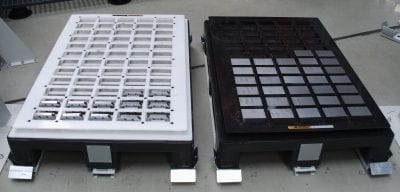
Gli stampi ALLMATIC per pallet per materiale grezzo e pezzi finiti sono progettati in modo ottimale per essere movimentati da un robot.
Quando arriva un ordine, il robot inizia la scansione del codice a barre della matrice del materiale grezzo e riceve così tutti i dettagli per il processo di produzione in corso. A questo scopo, il Manufacturing Management Software (MMS) di Fastems richiama automaticamente i programmi rilevanti per l’automazione e la lavorazione del pezzo. Con una pinza a magnete permanente, il robot recupera un pezzo grezzo dalla matrice e lo posiziona su un supporto di riafferraggio per posizionarlo con precisione. Successivamente, il robot trasporta il pezzo fino alla stazione di prelievo e carica il pallet della macchina utilizzando la pinza parallela.
Lavorazione completa con 2 processi di bloccaggio
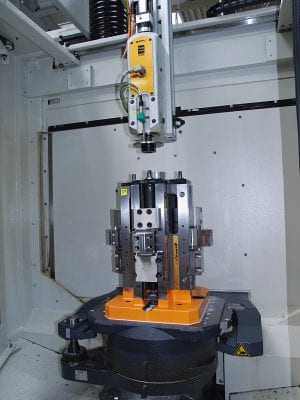
L’ALLMATIC Clamp Drive (sopra) rende possibile il montaggio di pezzi automatizzato.
Per qualsiasi processo di produzione corrente, sulla macchina sono sempre presenti 2 attrezzature in modo che la produzione possa essere continua e che sia possibile realizzare una lavorazione a 6 assi in sole 2 fasi di processo (OP10 e OP20). Il bloccaggio automatizzato e flessibile dei pezzi viene gestito dall’ALLMATIC Clamp Drive, montato sul lato robot del cambio pallet della macchina.
Un ordine di produzione inizia sempre con un pallet vuoto; i pezzi vengono bloccati sulla prima attrezzatura (OP10), mentre l’OP20 rimane vuoto durante la fase di lavorazione. Dopo il processo di lavorazione, i pezzi semipronti vengono temporaneamente immagazzinati davanti alla macchina per poi essere bloccati sulla seconda attrezzatura (OP20). Dopo la commutazione dei pallet, il robot può iniziare a caricare il primo dispositivo (OP10) con nuovi pezzi grezzi. Successivamente, l’intero ordine può essere elaborato con la rotazione continua delle fasi di processo OP10 e OP20. In occasione di un cambio di prodotto, il robot trasporta sulla macchina il portapezzi necessario per la produzione successiva, mentre le ultime parti dell’ordine precedente si trovano ancora all’interno della macchina.
Una volta che un ordine di lavoro completo è stato completato, il robot, se necessario, cambia automaticamente i pallet necessari per il nuovo ordine (nuovi pezzi) con dispositivi all’interno della macchina.
Potenziale per l’ottimizzazione dei processi
“Con una soluzione di automazione complessa come questa, dobbiamo ancora acquisire molta esperienza per essere in grado di identificare il possibile potenziale di ottimizzazione dei singoli processi”, sottolinea Herbert Mayr.
Attualmente, il robot rimuove tutti i pezzi semilavorati e li posiziona nella stazione di buffer, quindi carica l’attrezzatura OP20 con questi pezzi. Per la rimozione di tutti i pezzi, il pallet deve essere ruotato. Un processo di bloccaggio sicuro richiederebbe tuttavia il riferimento del Clamp Drive tra i bloccaggi ma ciò costa tempo prezioso. “Questo è ciò che vogliamo cambiare facendo rimuovere al robot prima un pezzo semipronto e poi facendogli caricare immediatamente l’attrezzatura con un nuovo pezzo grezzo nella stessa posizione di bloccaggio, senza bisogno di girare il pallet”, afferma Mayr.
La programmazione parametrica riduce al minimo
i tempi non produttivi
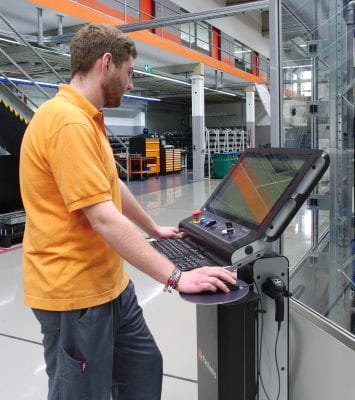
Questo è il dipendente responsabile del sistema ALLMATIC, in piedi accanto al terminale per l’MMS di Fastems, che tra l’altro si occuperà dell’intera pianificazione, del controllo e del monitoraggio del processo di produzione automatizzato. Oltre a ciò, non solo gestirà i programmi NC, ma anche tutti i 160 utensili e ne monitorerà i tempi di fermo macchina.
Poiché la cella di produzione agile di ALLMATIC è progettata per processi di produzione non presidiati per lunghi periodi di tempo, l’introduzione di nuovi pezzi, compreso l’adattamento della cinematica del robot, dovrebbe richiedere solo il più breve periodo di tempo possibile. La programmazione parametrica del robot tramite il Manufacturing Management Software (MMS) fornisce un supporto fondamentale per raggiungere questo obiettivo.
Non sono necessarie conoscenze speciali sui robot, spiega Luis Paiba e continua: “Fastems ci aveva già messo a disposizione alcuni programmi per la produzione dei pezzi in lavorazione in anticipo. Ogni volta che è necessario realizzare un nuovo pezzo, le necessarie sequenze di movimento possono essere facilmente regolate inserendo parametri specifici (fasi di manipolazione), senza dover eseguire l’apprendimento del robot, processo che richiede molto tempo. I nostri dipendenti hanno già utilizzato questo metodo per creare 17 nuove sequenze di movimento per il robot”.
Luis Paiba, Responsabile sviluppo e progettazione di ALLMATIC afferma:
“Se vogliamo diventare leader tecnologici, dovremo anche affrontare l’automazione in modo più intenzionale, non solo per quanto riguarda i nostri prodotti”.
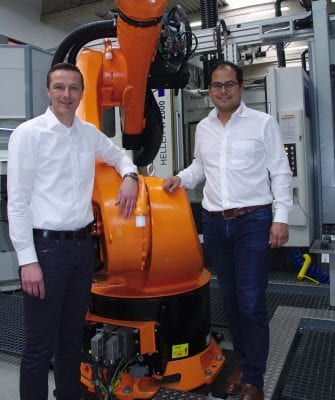
Herbert Mayr (a sinistra), Operations Manager e Luis Paiba, Responsabile sviluppo e progettazione, hanno acquisito una preziosa conoscenza durante il progetto.
Ripensamento e preziose intuizioni
L’utilizzo di questo sistema automatizzato ha consentito ad ALLMATIC non solo di ottenere risultati in termini di produttività e flessibilità nel processo di produzione, ma secondo Luis Paiba e Herbert Mayr, anche di acquisire preziose intuizioni.
“Tutti i pezzi che ora vengono prodotti con la cella robotizzata erano già stati realizzati da noi in precedenza. Come risultato dell’automazione, abbiamo dovuto cambiare il nostro modo di pensare e quindi siamo stati in grado di individuare nuove potenzialità per ottimizzare i nostri processi e le nostre procedure. A titolo di esempio, i pezzi possono ora essere completamente lavorati con 2 anziché 3 fasi di bloccaggio. Abbiamo adattato i nostri pezzi a questo scopo. Abbiamo inoltre aggiunto all’automazione processi di lavoro precedentemente manuali integrando nella cella una stazione di soffiaggio e rivestimento antiruggine”, sostiene Luis Paiba.
Herbert Mayr, Operations Manager di ALLMATIC afferma:
“Molti produttori scuotevano la testa alla mia idea di una soluzione per il cambio automatico. Ma con Fastems, abbiamo superato questa sfida proprio come altre”.
Non è solo una vittoria in termini di capacità
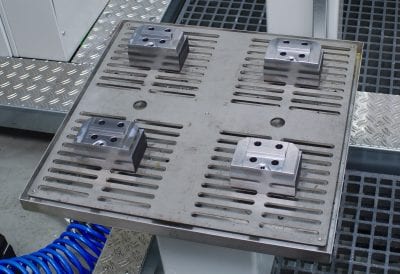
Questa è la stazione di prelievo con pezzi lavorati in precedenza. Attualmente, con la cella robotizzata vengono prodotti 32 diversi pezzi per morse di macchine, ad esempio ganasce, corpi di base o piastre di pressione e di bloccaggio, in lotti di oltre 100 per ordine.
Herbert Mayr ha acquisito un’altra intuizione cruciale:
“L’automazione assicura i lavori, poiché ora possiamo rispondere molto meglio alle fluttuazioni degli ordini. Al momento, la nostra cella robotizzata funziona a una capacità del 90%, producendo 32 diversi componenti non presidiati in 2 turni fantasma. Se il numero di ordini in arrivo dovesse diminuire drasticamente, non saremmo automaticamente costretti a tagliare i lavori, poiché la cella robotizzata potrebbe funzionare in un solo turno non presidiato”.
Cella robotizzata agile: caratteristiche principali
-
Grazie all’impiego dell’Heller H 2000 e di un magazzino di 160 utensili (con una capacità totale di 409 utensili) è possibile una lavorazione completa con 2 processi di bloccaggio. Questa immagine mostra un pallet macchina nell’area di lavoro del BAZ a 4 assi. Accanto a questa configurazione viene posizionato un altro pallet che rende possibile lo scambio di pallet in qualsiasi momento.
Una delle due stazioni di materiale, ciascuna per 2 europallet in plastica (per pezzi grezzi e finiti).
- Scaffali di stoccaggio per un massimo di 12 pallet macchina con portapezzi ALLMATIC
- ALLMATIC Clamp Drive per il bloccaggio e lo sbloccaggio dei pezzi
- Centro di lavorazione a 4 assi Heller H 2000 per la lavorazione di pezzi a 6 assi
- Kuka-Robot KR600 (peso di movimentazione max. 400 kg)
- Pinza e doppia pinza per pallet di Schunk per la movimentazione di pezzi (pinza a magnete permanente/pinza parallela)
- Stazione di trattamento antiruggine
- Stazione di soffiaggio
- Stazione di riafferraggio / buffer rack
- Cassetto per pezzi di misura
- Lettore di codici a barre
- Manufacturing Management Software (MMS)
per la gestione automatizzata del prodotto
Specialista per sistemi di bloccaggio
ALLMATIC è stata fondata nel 1973 ed è diventata un fornitore leader di sistemi di chiusura dal 2001, anno in cui è entrata a far parte del Jakob Group. Fabbrica prodotti come semplici mandrini meccanici filettati, morse NC (cioè morse con amplificatori di potenza) e morse Gripp, ad esempio per la lavorazione a 5 assi, nonché soluzioni di bloccaggio multiple e speciali.
L’azienda ha attualmente 73 dipendenti, tra cui 16 apprendisti, e sviluppa e realizza soluzioni innovative per il mercato mondiale presso la sua sede centrale di Unterthingau, nella regione dell’Algovia. Il mercato principale è l’Europa, soprattutto la Germania, seguita da Austria, Italia, Francia e Romania. Nel 2018, ALLMATIC-Jakob Spannsysteme ha generato un fatturato di circa 10,8 milioni di euro.
Originariamente pubblicato su NC Fertigung, edizione 07-08/2019